Learn how to use MCMS
Summary
Get Started
Database choice
Your data are yours no matter the database you choose
The application requires a connection to a database in order to work. The first time that the app is started, it will ask you to setup the connection. The available options are SQLite and Microsoft SQL Server.
SQLite
Easy as creating a file
Nothing to install
Ideal for local deployment
Handles small number of concurrent users
Does not support encryption
SQL Server
Supports a large number of concurrent users
Supports encryption and advanced security features
Fastest query execution
Requires a running instance of Microsoft SQL Server
Harder to configure
Database Configuration
Make your manufacturing cycle management system up and running
- Click on the SQLite button to open the configuration form;
-
Fill the
Data source
with any path on you machine or on you company network and specify a file name.- For example
D:\DataBase\MyDataBase.db
; - If the database already exists the application will connect to it otherwise it will be created;
- More on connection string;
- For example
- Click on confirm and the application will inform you that it needs to be restarted;
- Confirm again and the application will close;
- Download and install Microsoft SQL Server or SQL Server Express if do not have any server already installed;
- Click on the Microsoft SQL Server button to open the configuration form;
-
Fill the
Data source
field with server address.- For example (SQL Server Express)
(LocalDb)\MSSQLLocalDB
; - More on connection string;
- For example (SQL Server Express)
-
Fill the
Initial catalog
filed with the name of the database.- If the database already exists the application will connect to it otherwise it will be created;
- Complete the form with the rest of the information based on your server configuration;
- Click on confirm and the application will inform you that it needs to be restarted;
- Confirm again and the application will close;
Example database
Sometimes an example is better than 1000 words
Download the SQLite test database to see some action right away. Connect the software to this database and start exploring. You can create, delete, edit, do whatever damage you want and you can always revert it by downloading it again. This is the best way to try out the full extent of the software consequence freely.
Core Concepts
Company
How your business is structured
The company represents the operations your business can perform. The departments divide the company into different units, which could be separate facilities or various services your company offers. The areas serve as specialized subunits within these departments, grouping similar operations and often led by an area manager driving the team’s performance. The stations represent the workstations contained within an area.
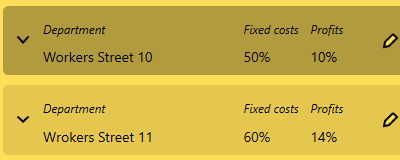
Departments
For example, you might have Facility A, Facility B, etc. Or you may have the production department, the sales department, etc. The key property of a department is having a layout.
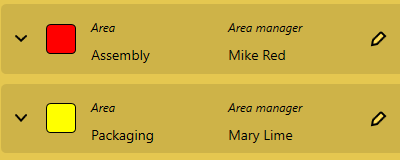
Areas
Inside a department you might have one or more areas. For example, a department might have the assembly area, the painting area, etc. The key property of an area is having a manger.
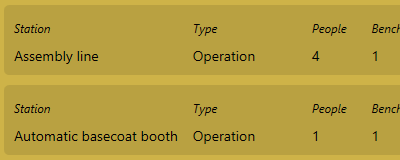
Stations
The stations are where the work is done. They might represent a machinery, a desk, etc. They might have one or more employees working on them. There could be also a set of identical stations in an area.
Steps
What your company does
The steps encompass the operations your company can perform. They are executed at the stations, and a sequence of steps is called a working cycle. Each step may have one or more requirements, which could potentially lead to failure modes that allow for identifying causes and effects. For each cause of failure, one or more preventive actions can be determined. Additionally, the steps might necessitate one or more controls on the product or process. These controls typically mirror the requirements and generate control plans for the working cycles.
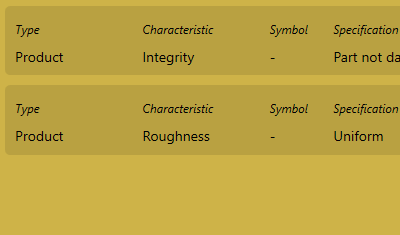
Controls
The controls on product might be visual, dimensional, etc. The controls on the process might be the temperature, the pressure, etc. They will build the control plans for the working cycles.
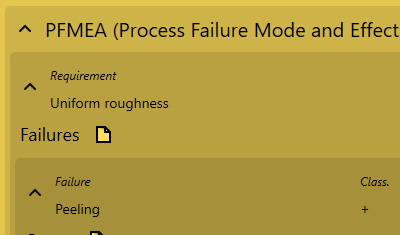
Risks
The requirements, failure modes and causes are your PFMEA. The risks are evaluated by an index and a priority. The priority is designed to account for severity relatively to occurrence and detection.
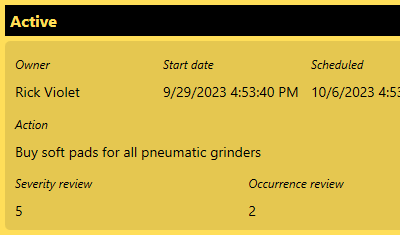
Opportunities
The actions based on the risks analysis lead to opportunities. The actions are directly related to failure causes and automatically review the risks indexes. Your PFMEA will be always up to date.
Products
What your company sells
The products represent the goods or services that your company provides. They can be customer-specific or standard. It is best to have standard products rather than customer-specific ones to reduce complexity. For each product, you might have one or more cycles that represent the operations needed to produce the product. Having well-defined company structures and steps is crucial for a realistic cost estimation. The cost estimation is done by considering the time and resources needed to complete the working cycles. For each step of the cycle, you might have one or more materials that are consumed in the process. Additionally, there might be external processing steps within the working cycles, which refer to outsourced operations.
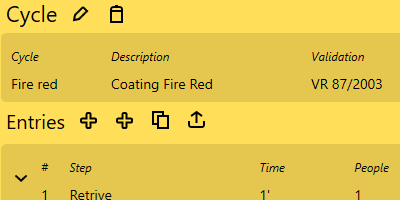
Costs
Each step of the working cycle has time, people and parts parameters. The time is how long a step takes to be completed in minutes. The people is the number of employees that concurrently work on the batch. The parts are the number of items that are produced in the step also called batch.
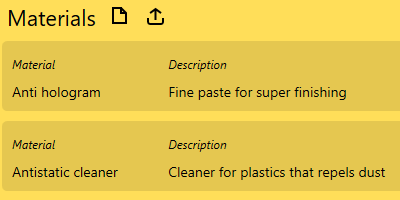
Materials
The materials are mainly the consumables and the raw materials that are used during the working cycles. They can be part scoped or batch scoped this affect the cost estimation.
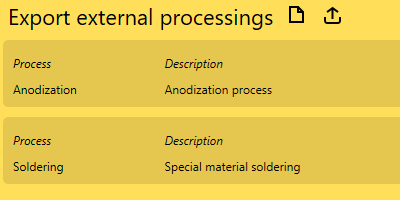
External Processing
These are the operations that are outsourced. They are defined as a cost per part with no other parameters. This means that they are a flexible way to add costs to the working cycles with no strings attached.
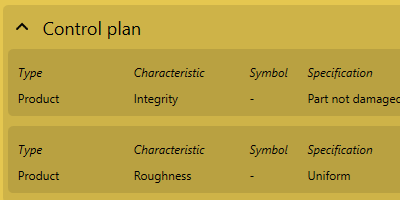
Control plans
For each cycle the control plans are generated from the requirements and the controls. This is convenient so that the control plans are always up to date with the working cycles. By making this information available anybody can verify the products requirements.
Customers
Plan what you are gonna deliver
The customers are the entities to whom you deliver your products. This section is meant to gather essential data about which products you sell and to whom. Each customers might place one or more commissions, reflecting their tailored orders. These commissions encompass initial start-up entries for any preliminary costs, up to shipment costs. All elements of a commission -such as products and work cycles, start-ups, and shipments- can be used to create a price offer for the client.
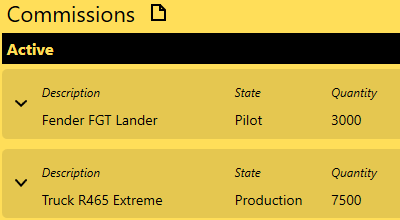
Commissions
The commissions are very flexible and can be matched with the orders that the customer makes but is not strictly necessary. They can have quantity, start date and due date, but those values are just for record. Commissions can be marked active or expired.